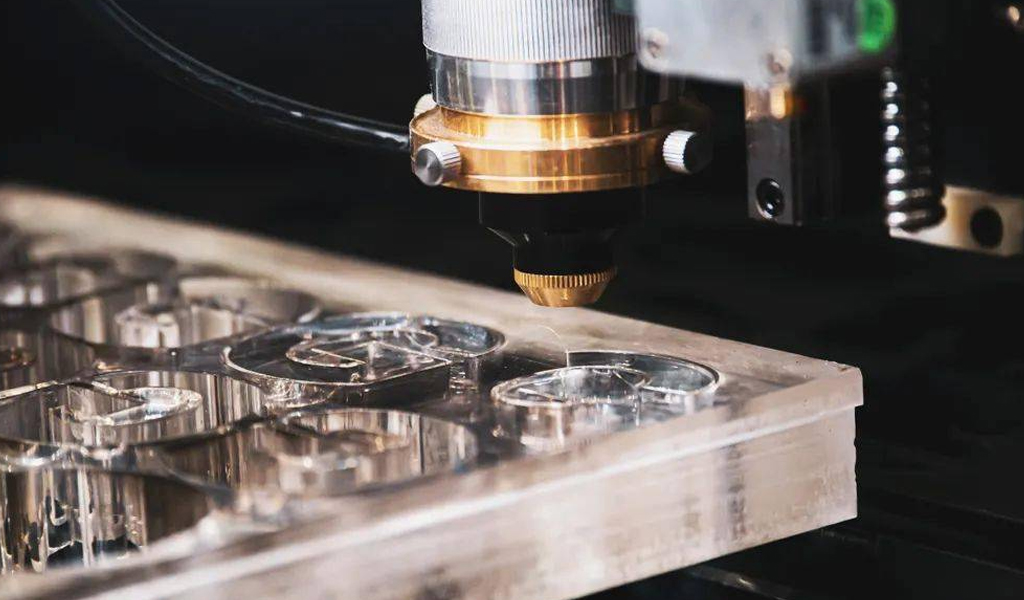
Understand Interventional Medical Stent Laser Cutting Material and Physical Properties
The purpose of this article is to define how scaffold performance depends on the material properties and physical properties of the tubing used to produce the device. This information will guide the rack designer in specifying tubing materials to achieve the desired device performance. The “ideal scaffold” is introduced before comparing existing scaffold materials with candidate scaffold materials. Since most stents are fabricated from metal tubing, the required tubing properties are also discussed to show how they interact with stent performance and manufacturability. The various tube manufacturing methods that achieve these properties are also briefly reviewed.
1. Introduction
Newer generations of stents are emerging with claims of improved stent performance based on material properties. For example, when promoting its new Vision stent, Guidant said: “The Vision stent is laser cut from a cobalt-chromium superalloy, which allows us to reduce stent thickness and overall stent thickness without compromising radial strength or radiation capabilities. volume. The results? Extraordinary delivery capabilities and optimal clinical outcomes.” Likewise, Medtronic describes its Driver Coronary Stent System as follows: “Cobalt-based alloy, unique modular stent design and stent laser cutting. The Driver Coronary Stent System is manufactured by Composed of an ultra-thin stent and the company’s proven 10-crown design. The combination of these unique design features provides physicians with the additional flexibility needed to navigate tortuous anatomy and reach hard-to-reach lesions. Due to its cobalt-based The density of the alloy is higher than stainless steel, so the Driver maintains optimal radiolucency.”
Some device performance characteristics do relate directly to materials. Biocompatibility, X-ray and MRI visibility, radial strength, acute and chronic recoil, axial and radial flexibility, delivery capacity, shape and long-term integrity, all depend on the material’s mechanical and physical properties. Therefore, it makes sense to try to describe the ideal scaffold material and review how the various available materials compare to the ideal situation. Given that the most common material form of stents is tubing, this article provides a review of how tubing properties impact stent performance and manufacturability.
2. Ideal scaffold material
The ideal stent material is completely corrosion-resistant, compatible with blood vessels, resistant to fatigue, and can be visualized using standard X-ray and MRI methods. Additionally, the specifics of balloon-expandable or self-expanding stents need to be considered.
For balloon-expandable stents, infinite elastic modulus prevents retraction. The lower yield strength allows the stent to expand under acceptable balloon pressure and facilitates crimping of the stent to the delivery system. High tensile properties after expansion help achieve radial strength with minimal implanted foreign body volume. Higher stretch properties also allow for the use of thinner stents, resulting in a smaller overall profile, thereby improving flexibility, delivery capacity and access to smaller vessels. Steep work hardening rates allow for ideal strength gains during expansion. Finally, high ductility is required to withstand deformation during expansion.
The above characteristics are interrelated and sometimes contradictory and require careful compromise. For example, materials with higher tensile strength generally also have higher yield strengths. While higher tensile strength is beneficial in increasing radial strength as discussed above, the associated higher yield strength can produce undesirable and severe retraction when the balloon is deflated.
For self-expanding stents, large recoverable strains are required for expansion and resistance to extrusion. This is often described as hyperelastic behavior, with the ideal stress-strain curve showing a long and high plateau after an initial elastic loading phase. Inside the delivery catheter, the device remains in the superelastic range and may reenter the superelastic range after deployment if sufficient deformation occurs due to vascular interactions or external forces. Elongation and tensile strength are of great importance during scaffold fabrication, but they have received less attention than the hyperelastic events themselves. To the extent that these traditional properties influence fatigue resistance and fracture toughness, elongation and tensile strength should be considered important parameters. Resistance to pulsation fatigue and bending fatigue is critical for stents because they move with the blood vessels.
It is currently controversial that the eccentric stiffness of superelastic NiTi alloys arises from the hysteresis effect between loading and unloading paths. It has been suggested that a larger hysteresis effect helps increase resistance to compression and reduces retraction after the balloon is deflated. On the other hand, the lack of hysteresis effect allows the stent to have squeezable/recoverable vascular compliance similar to that of natural healthy blood vessels, which may reduce damage to tissues near the stent.
3. Compare implant grade and other possible metal materials
Other alloys and metals have also been added, given that the properties of these materials may make them attractive candidates for future stent use. Of course, properties such as biocompatibility and fatigue resistance of these materials require investigation and are beyond the scope of this article. With the exception of NiTi alloys, the properties listed are for the fully annealed condition where high ductility is achieved. The properties of three possible NiTi (used for nitinol laser cutting)variants are demonstrated, including the commonly used superelastic state, the martensitic state and the cold-worked version. All materials are non-ferromagnetic and therefore safe for use in magnetic resonance imaging (MRI), but this does not mean they do not produce artifacts. Considerable work is currently underway to evaluate and develop materials that can minimize artifacts to benefit from MRI’s tissue contrast, lack of radiation, and the possibility of assessing intra-stent blood flow. However, there is currently no material property that can be considered to accurately predict artifact-free visualization.
Density is reported to describe radiographic visibility, and generally denser materials improve visibility. The elastic modulus E is a key parameter describing radial strength (a function of E x t , where t is the tube wall thickness), buckling resistance (proportional to E x t³) and springback. The ultimate tensile strength (UTS) and 0.2% yield strength are used to describe the mechanical strength of the material, while their distribution is used to illustrate the slope of the work hardening curve that affects the deployment force and deployment stent strength. Elongation at break is used to express toughness. Finally, the ratio of yield strength to elastic modulus is given to characterize the elastic range of the material, which affects acute rebound and radial strength. The elastic range of nitinol is defined as the maximum recoverable strain and quantifies its superelastic behavior.
Although 316L does not have strong radiographic visibility, it is still used as a reference material for stent applications. By enriching nitrogen and replacing nickel (using manganese), nickel-free stainless steels can achieve significantly higher strengths while other properties remain very similar. Additionally, manganese-chromium austenitic stainless steel eliminates concerns about allergic reactions to nickel.
Compared to stainless steel, cobalt-based alloys exhibit higher density, elastic modulus, strength, and differences between yield strength and ultimate tensile strength, but relatively similar toughness. Among the cobalt-chromium series, L605 alloy has the highest these properties. Given the current interest in this alloy as a stent material and the fact that stainless steel has been the primary material for balloon-expandable stents, we conducted a more in-depth study of the properties of these two alloys.
Additional observations from the same tensile tests provide an interesting perspective on radial forces. The radial force depends on the flow stress after expansion. Interestingly, the stress of L605 at 30% strain is 66% higher than that of 316L at the same strain level.
Finally, the slope of the curve in the stage after the yield point where strain hardening occurs is considered. L605 strengthens at 15 MPa/% strain, while 316L is 9.6. As flow stress increases rapidly, local strains will tend to propagate along the length of the strut because the initial deformation site rapidly intensifies. In contrast, materials with shallower slopes tend to deform locally in areas of stress concentration.
To date, titanium group materials have not been used in stents, despite their reputation as biomaterials and their good MRI visibility. Pure titanium’s low density, elastic modulus and strength hinder its use. Alloy α-β grades increase strength but negatively affect elongation. Furthermore, the combination of higher strength with low modulus increases the elastic range; therefore recoil does not achieve sufficient recoverable strain to allow self-expanding use. There may be some potentially interesting beta or near-beta titanium grades with improved density, ductility and strength. Their high strength and elastic range have found applications in orthopedics and orthodontics.
Refractory metals such as tantalum and niobium have been used in stents, with tantalum receiving particular attention due to its combination of high radiopacity and good MRI visibility. Also note that tantalum exhibits the smallest elastic range of all the materials in Table 1, which helps minimize kickback. Tungsten and molybdenum are also included in Table 1 to demonstrate their superior E-modulus and strength. Also note that tungsten is very dense. Although their use as pure metals is not envisaged for stents, their properties as alloying elements are promising. Several of these refractory metals are beta titanium stabilizers. Finally, refractory metals have minimal MRI artifacts.
The mechanical properties of pure precious metals are rather weak, but platinum containing 10% iridium has been used in stent applications. An iridium content of 20% or alloying with tungsten can further significantly increase strength and achieve similar ductility. The special densities of platinum, iridium, and gold make them the materials of choice for improving the radiopacity of other alloys, with Nitinol and stainless steel also reported to have this property. Palladium-based alloys are described as minimizing MR artifacts, having improved radiopacity and similar strength compared to stainless steel.
The mechanical properties of pure precious metals are rather weak, but platinum containing 10% iridium has been used in stent applications. An iridium content of 20% or alloying with tungsten can further significantly increase strength and achieve similar ductility. The special densities of platinum, iridium, and gold make them the materials of choice for improving the radiopacity of other alloys, with Nitinol and stainless steel also reported to have this property. Palladium-based alloys are described as minimizing MR artifacts, having improved radiopacity and similar strength compared to stainless steel.
Cold-worked Nitinol exhibits surprising Hookean elasticity, allowing large recoverable strains of up to 4% to 6%. The UTS is quite high and has similar ductility to superelastic Nitinol. Its properties are independent of temperature. These special features may lead to some creative designs.
The last one shown is a common magnesium industrial alloy. The corrosion behavior of magnesium-based alloys is the source of current research on bioresorbable scaffolds. However, the density and mechanical properties of this material are very low compared to any scaffold material currently in use.
Finally, because no material yet exhibits all desirable properties, compromises must be made, sacrificing some properties for others. For example, nitinol stents are made from a rather low ductility material, with elongation at break typically less than 15%. However, proper design can achieve incredible expansion rates without breaking. Another avenue for tailoring material properties to the specific requirements of vascular implants is through innovative alloys. The aforementioned improvement of radioactive toughness by adding dense elements is one example.
4. Ideal pipe properties
Most brackets are cut from tubing. In addition to the inherent material properties discussed previously, some tubing properties can have a significant impact on the performance and manufacturability of stents. Important ideal pipe properties are described below.
The choice of melt source is extremely important. The nature and purity of the elemental material components mixed prior to melting, as well as the melting method itself, have an impact on the uniformity, porosity and micro-cleanliness of the cast alloy.
Although ASTM and ISO standards set limits, these limits are often insufficient to achieve the safety required for stent applications.
This is especially true when it comes to micro-cleanliness. Taking stainless steel as an example, both ASTM F138 and ISO 5832-1 standards allow heavy inclusions up to Level 1 and inclusion thickness up to 15 µm for a length of 75 µm. This drawback is huge compared to stent struts that are less than 100 microns thick. These inclusions pose a serious threat to expansion rupture and premature fatigue failure of the stent. At present, with the improvement of material strength and the development of small vessel stent technology, the size of stent struts is also constantly shrinking, and the influence of inclusions is becoming larger and larger. When selecting material sources, attention should also be paid to the uniformity of the chemical composition. Its consistency during different heating processes will be beneficial to obtain uniform mechanical properties and electropolishing reactions.
Tubing is usually produced in welded-drawn or seamless form. Although modern welding equipment and continuous online inspection systems are very robust, there is still no guarantee that the weld will be completely defect-free and free from localized micro-contamination and segregation. Traces of lubricant on the strip are sufficient to cause irreversible carbon enrichment in the molten material, leading to unacceptable risks of corrosion and embrittlement. Therefore, tubing for stents and other implanted devices should be seamless.
Second, the tube drawing process needs to be adequately controlled to ensure repeatable tube properties. Stainless steel is less sensitive to processing parameters, while L605 and Nitinol are more difficult to control and their properties will vary greatly depending on the processing process. This sensitivity provides the opportunity to tailor material properties to equipment requirements, but only if the pipe manufacturer understands the detailed properties of the material and tightly controls the processing process.
L605 is very sensitive to heat treatment conditions. An annealing study was performed on 35% cold worked tubing according to the alloy supplier’s recommended time and temperature range. The time varied between 2 and 20 min and the temperature between 1100 and 1200°C. Tensile test results and microstructural examination showed large differences in the following ranges: UTS 819 – 1117 MPa; 0.2% yield strength 380 – 648 MPa; elongation 35 – 56%; grain diameter is 5.6 – 89.8 microns.
Another complexity with Nitinol is the interaction between the delivered tubing and the thermomechanical stent shape setting. Furthermore, a specific set of pipe properties can be obtained through different combinations of process parameters, such as cold working and hot straightening. These seemingly similar tubes may react differently during stent shape setting operations. It is therefore reasonable to specify pipe properties after a defined thermal post-treatment rather than at the time of drawing. Furthermore, it can be noted that scaffolds cut from large tubing require only one shape setting step, with minimal deformation and limited thermal exposure. This approach offers the opportunity to achieve a more uniform and controllable structure than scaffolds that are expanded in multiple steps from small tubes. A previous paper compared these alternative nitinol stent manufacturing methods in detail.
Microstructures with uniform, equiaxed small grains are generally preferred for polishing and fatigue and corrosion resistance. Likewise, the limits set by ASTM and ISO standards are not optimal for braces. The commonly specified ASTM grain size limit of 5 corresponds to a grain diameter of 63.5 µm, which for the thinnest scaffolds could result in a single grain passing through the wall, which is clearly an unacceptable situation. But minimizing grain size may not be the ultimate goal, as it also affects mechanical properties and polishing. It generally increases yield strength and negatively affects backlash during crimping and expansion. Here again we need to find a compromise.
Dimensional accuracy is key to stent performance and manufacturability. To evenly deploy the stent, wall thickness consistency is required. Achieving consistent pillar widths in laser cutting is critical. If a constant laser beam energy hits different walls, it will tend to cut wider grooves where the walls are thinner and potentially damage the other side of the pipe. The accuracy of cutting brackets depends on the tube manufacturer’s ability to maintain minimal variability and minimize the offset between the average and nominal dimensions for which the laser settings are optimized. . Wall tolerance and concentricity requirements should be specified. Note that tight tolerances mean that wall measurement systems are accurate enough to favor the use of hard contact gages over optical systems. The outer diameter (OD) plays an important role in the guidance of the pipe under the laser beam. Narrow tolerances and tight cylindricity facilitate laser cutting accuracy.
The surface finish should be consistent with the desired stent finish obtained after cleaning and electropolishing steps. These operations vary between stent manufacturers depending on the target material removal for the respective process. This results in different surface requirements for the original pipe. The inside diameter surface is generally more critical because it removes less material than the outside diameter surface. Finish is typically specified by surface toughness (Ra) and limits on defects such as pull marks and scratches, which can be defined by visual criteria that set acceptance limits.
Dimensional accuracy and surface finish vary widely depending on the tube process and drawing alloy type. Figures 2 and 3 illustrate various drawing processes. Floating and fixed plug drawing processes achieve optimal geometries and surfaces as long as they are matched to the material, dimensions and temper. Hard core die drawing is an alternative method often used in situations where the plug doesn’t actually work. This is often related to the behavior of the tool/material interface, where certain alloys are prone to sticking and seizing. Some materials, including Nitinol, require an oxide layer as lubricating support. The oxide layer is less ductile and may crack under stress from drawing and heat treatment. Unless properly controlled, these cracks can propagate through the bulk material with devastating effects. The oxide layer can be removed from the inner and outer diameters by polishing or etching. However, most stent cutters prefer to leave the oxide layer on the inner diameter because they find the slag generated by the laser is easier to remove. In addition, ductile core stretching technology is used. In this technique, a mandrel is introduced into the tube blank and remains inside the tube during a continuous drawing and annealing process. At the end of the process, the mandrel is removed by stretching. In ductile core drawing, tube wall accuracy depends on the consistency of the tube’s toughness. Finally, while fully annealing is the standard condition for the bracket itself, cold working the tubing is preferred during laser cutting and then annealing the bracket later in the process. This method helps prevent damage to the fragile annealed tube, and post-cut annealing also helps relieve residual stress created during the laser cutting process. The final annealing requires careful control to obtain the desired mechanical properties and microstructure.
Figure 2: Hard Tool Drawing Technique: The outer diameter, inner diameter, and walls are created by contact with a rigid tool that does not deform during the drawing process.
5. China Best Stent Laser Cutting Manufacturer
This article describes and discusses the properties of various metallic materials in conjunction with the properties of ideal scaffold materials. It then explains how the pipe properties affect the performance and fabrication of the bracket, providing a basis for designers to correctly specify the required pipe parameters.
Be-Cu specializes in high precision laser tube cutting for simple or complex devices on a wide variety of materials. Our advanced laser tube cutting services combine robust laser cutting tools with innovative laser cutting methods, to produce the most demanding geometries for cutting-edge applications.
Be-Cu specializes in superior laser tube cutting that can be used for a wide variety of applications including:
- Stents
- Hypotube Shafts
- Pull Wire Rings
- Markerbands
- Electrode Rings
- More medical laser cutting service
Be-Cu offers a full range of laser processing technology such as: ablation, laser marking, tube cutting, and wire stripping. Our experienced engineers and innovative laser processing systems, allow us to offer optimal laser solutions for the most complex applications with industry standard lead times.
Our company has created parts for over 500 companies and offered them the best Service.Be-Cu provides the highest standard of micro laser cutting service for all your needs. Contact us today to know more about what we offer!
- Sales: Bella
- Web:be-cu.com
- Phone: +86 151 1280 7161
- Email: [email protected]
- Affiliated: Be-cu Prototype
- Address: Dongguan,China